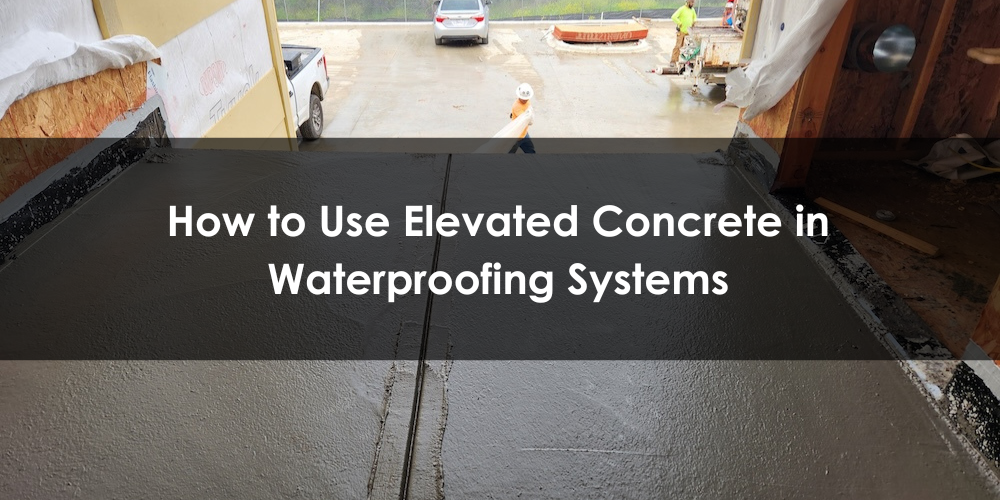
Exterior balconies, breezeways and stair landings exposed to the weather in multi-family construction need to be waterproofed to prevent costly leaks and moisture damage. Elevated concrete is typically applied on top of waterproofing membranes for reliable and cost-effective protection.
In this article, the Nettles experts explain why waterproofing is important, what waterproofing systems consist of, and how elevated concrete is installed.
What is waterproofing used for?
Waterproofing is commonly used under concrete wear surfaces on multi-family structures with wood-framed balconies, breezeways, and other spaces open to the elements. Waterproofing systems prevent rain and other moisture from entering the interior of the building and creating mold.
Waterproofed balconies or breezeways must have a ¼” slope per foot away from the building to allow water to run off them.
What does a waterproofing system consist of?
Waterproofing contractors cover the wood joists and plywood with a waterproof membrane and install a flashing system at the exterior wall and any other potential leak areas. Then, a layer of concrete is poured to create a flat walking surface that requires minimal maintenance.
Some waterproofing systems use a fluid-applied coating directly adhered to the plywood substrate instead of a sheet material. This coating is brushed on like paint and provides an extra layer of waterproofing protection.
How is elevated concrete installed?
Elevated concrete is poured over the waterproof membrane. This concrete is often called “lightweight” concrete. However, elevated concrete is normal weight (does not use a low density aggregate). It is commonly poured more thinly and mixed with fiber for added strength.
Elevated concrete contractors use a specialized pump and long hoses to pour the pre-mixed material to the correct location.
Can waterproofing systems be installed on existing structures?
Elevated concrete waterproofing systems are more commonly used for new construction. Waterproofing/concrete can be added to existing structures, but only if they can support the weight of the concrete.
What factors influence the cost of waterproofing/concrete systems?
The cost of waterproofing/concrete depends on the size and shape of the area(s), as well as the thickness, the required finish, and whether any color is added to the concrete.
Lower-cost waterproofing systems are typically thinner and more vulnerable to sunlight and moisture deterioration. More expensive waterproofing systems have failsafes built in to prevent leakages and structural damages.
Ready to learn more?
The Nettles team has decades of experience completing successful commercial construction projects across the Midwest and Southern United States, with offices in Kansas City and Houston. Contact us to discuss your next project!