Flowable Fill and Cellular Grout
What is engineered flowable fill?
Also called lightweight cellular concrete, cellular grout, low-density cellular concrete (LDCC), or controlled low-strength material (CLSM), engineered flowable fill is a mixture of Portland cement, water and preformed foam. The foam creates a structure of discrete air cells within the concrete, increasing volume, reducing density and improving flowability. Mix designs may use fly ash, sand and other aggregates to achieve specific densities and strengths. These properties make flowable fill ideal for a variety of geotechnical applications.
To install flowable fill, the Nettles team takes raw cement in powder form, mixes it with water in a pump to make a slurry, and pumps the slurry through the worksite with a hose. Alongside the hose, a mixer mixes the foam and adds it to the concrete slurry, creating the engineered fill material. The entire process requires only 4 or 5 crew members–resulting in a leaner workforce compared to other types of fill, since engineered fill pours do not require a dozer or a backhoe.
What are the advantages of flowable fill over traditional concrete or earthen fills?
Engineered flowable fill offers a number of benefits over other materials, including:
- Fast installation: Since flowable fill is self-compacting, it hardens within 90 minutes and is completely ready to go within 24 hours, saving you 30-50% of total construction time.
- Can be poured into very tight or constrained areas: Because of flowable fill’s light weight and high flowability, it can be pumped from up to a thousand feet away and can be poured even into very narrow or constrained spaces.
- Light weight and high strength: Nettles flowable fill is about one third to one half the weight of normal concrete or earthen fill. This light weight makes flowable fill especially important for soil erosion. If the fill is too heavy, it can slough off and cause erosion and sinkholes. Flowable fill is light, and yet extremely strong and durable.
Want to learn more?
Read our comprehensive flowable fill buyer’s guide to learn more about what flowable fill is, how it’s used, and what you should know before purchasing.
Applications of flowable fill
When new utility piping is tunneled underground or installed in a casing, the space around it must be grouted. Flowable fill is highly flowable, making it an ideal solution for these annular space fills. Flowable fill also has a very low set temperature compared to traditional grout, which protects the new pipe from heat damage. Buoyant forces are also reduced during grouting, due to flowable fill’s low density.
Flowable fill is a quick and affordable solution for pipe trench fills and shaft backfills. Many use it as a permanent design feature; however, due to its low density, it can also be easily excavated for future maintenance and repairs.
Mechanically Stabilized Earth (MSE) backfills and Reinforced Soil Slope (RSS) Wall backfills are an excellent application for flowable fill, which reduces lateral forces on adjacent structures. Once cured, flowable fill has very low permeability, reducing the lateral pressure associated with water intrusion.
Flowable fill can be designed to meet load parameters and restrictions. Typically structurally supported plaza decks allow minimal loads, and can be highly complex and intricate. Flowable fill is an excellent choice for these applications as it will eliminate or reduce stress both in design and construction.
Flowable fill can be used to reduce overburden and evenly distribute loads over poor soils. The mix design can also be customized for specific location and geomaterial behavior.
Under the covering of asphalt paving most streets and roadways is 4-6 inches of granular rock or concrete material that can withstand the weight of traffic. Due to its lighter weight and lower density, controlled low strength material is the perfect roadway substrate for areas with poor soils or where the road needs to be raised out of a floodplain.
Abandoned gasoline, diesel, and oil tanks beneath gas stations or rural areas can be up to 2-3 thousand cubic feet in size. Flowable fill can be pumped from a substantial distance and is highly flowable, making it a good solution for fuel tanks and other underground void fills.
Why choose Nettles as your engineered flowable fill contractor?
Nettles Construction Solutions is one of the largest and most well-respected contractors and installers of flowable fill in the country. We have decades of experience with the material and pride ourselves on our best-in-class service. Our teams are experts in mix designs, working with different materials, and pumping the material correctly and precisely. With our 40+ years of experience, we’ve poured flowable fill in a huge range of applications, environments, and contexts–meaning that no matter the specifics of your project, we will be able to complete the pour efficiently, effectively, and expertly.
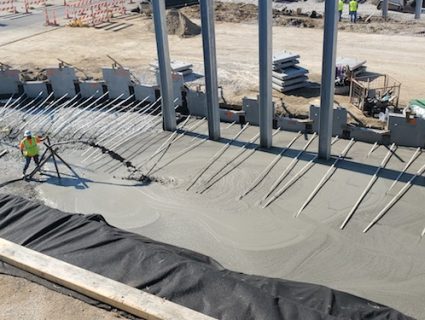
Flowable fill FAQs
No–the Nettles team will bring the material and install it ourselves.
Nettles flowable fill is about one third to one half the weight of normal concrete or earthen fill.
We can pour flowable fill in injection sites up to 1000 feet away from the pump.
We don’t pour when the temperatures are below freezing; however, we can pour flowable fill in environments up to 110 degrees Fahrenheit.
Our pricing is determined by the volume of material required and the number of equipment setups needed.
Yes! Since flowable fill is self-compacting, it hardens within 90 minutes and is completely ready to go within 24 hours, saving you 30-50% of total construction time.
We can install flowable fill in the entire eastern half of the United States, from the Gulf of Mexico up through the Dakotas, and as far west as Oklahoma.
Talk to an expert
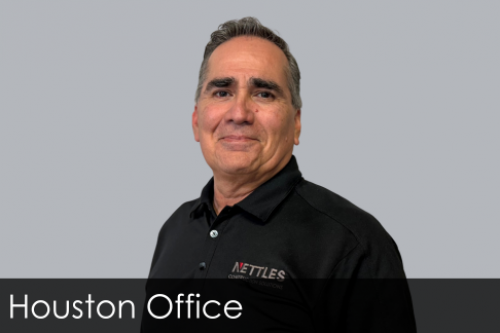
Ron Contreras
346.831.8998
ron.contreras@nettlescs.com
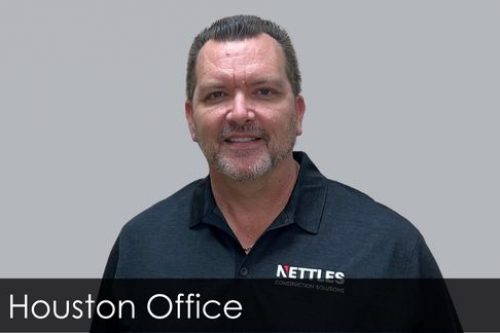
Bryan Batchman
979.451.8600
bryan.batchman@nettlescs.com
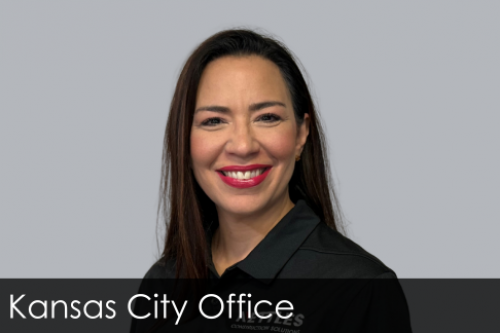
Ileana Perez
816.886.8658
ileana.perez@nettlescs.com
Have questions?
"*" indicates required fields